You are here - Engineers' Data > Hose Routing
Hose Routing
|
Hose Routing and Installation
|
|
Improper installation and routing of hose assemblies is one of the major causes of premature hose failure.
Below is a guide to best practice when installing and routing hydraulic hose assemblies.
|
|
1. Hose Length
|
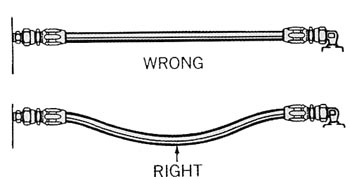
|
When pressurised, a flexible hose assembly can change length by as much as +3% or -6% compared
to its original length.
Always provide some slack in the hose to allow for this shortening or elongation however,
excessive slack in hose lines may cause poor appearance.
|
|
|
2. Hose Rotation
|
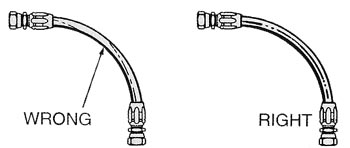
|
If a hose is installed with a twist in it, operating pressure will try to force it straight. This
can loosen the end fitting nut or cause reinforcement separation which can result in hose failure at
the point of greatest stress.
The printed layline on the hose is a good indication of this. If twisted and the assembly includes
a swivel nut end fitting, loosen the swivel nut, untwist the hose, and retighten the nut.
An assembly with two elbow end fittings will twist if the end fittings are not in proper
relationship to each other.
|
|
|
3. Ambient Heat
|
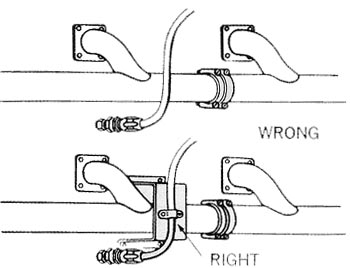
|
Exposure to high external ambient temperatures can dramatically shorten hose life.
Always route hose assemblies away from heat sources or install a protective sleeve or baffle
plate.
|
|
|
4. Abrasion
|
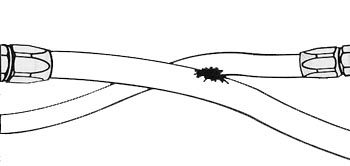
|
Constant abrasion at the same point on a hose can wear through the outer cover and eventually
weaken the reinforcement.
Hose assemblies should be routed to avoid abrasion with sharp objects, moving parts or other
hose assemblies.
The use of hose clamps can help to prevent abrasion.
|
|
|
5. Minimum Bend Radius
|
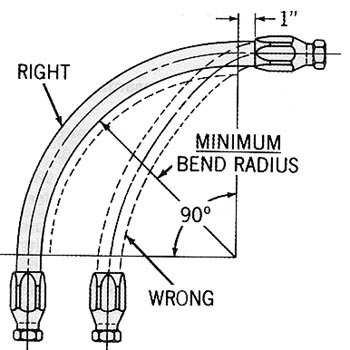
|
At bends, always provide sufficient hose so that it does not have a bend radius less than its
recommended minimum bend radius. Allow at least 1" (25mm) of straight hose out of the fitting socket
before it starts to bend.
Too tight a bend may kink the hose and restrict or stop the fluid flow. It also creates unnecessary
stress on both the hose and end fittings which can lead to reduced hose life.
In many cases proper use of adaptors and hose fittings can eliminate tight bends or kinks.
|
|
|
6. Vibration and Flexing
|
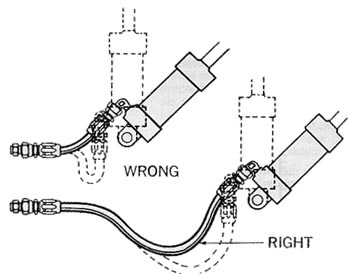
|
In applications where there is considerable vibration or flexing, allow additional hose
length.
The metal hose fittings, of course, are not flexible, and proper installation protects
metal parts from undue stress, and avoids kinks in the hose.
|
|
|
7. Appearance
|
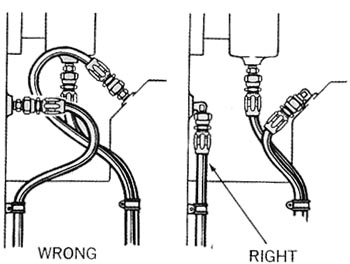
|
Routing for good appearance often means better functioning and easier inspection and maintanence.
It also often results in the use of less hose and fewer connections
1. Route hoses in straight lines or along machine contour 2. Route hose lines
together and in parallel to reduce abrasion 3. Use brackets and clamps to keep
hoses in place 4. Use hose assemblies of proper length. 5. Use elbow
adaptors and fittings for more direct routing
|
|
|
8. Use of Adaptors
|
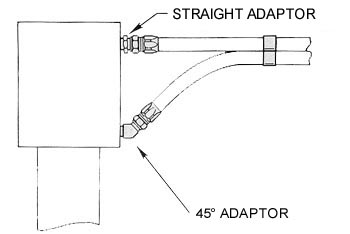
|
Adaptors have many purposes when installing hose assemblies. These include joining hoses to
a component, connecting two or more hoses together and changing the size or thread of a connection.
They come in many configurations and when used effectively, can help tidy up an assembly,
increase accessibility, reduce bends and general extend the hose life.
|
|